High Quality
Production Systems for
Optical, Technical and Crystal
Glasses
Hot-End Technologies
Stem-Welding and Stretching Technologies as well as Moil-Removal Functions
füller hot-end processing system with designated functions of welding, stretching or removing a moil follow the mature blowing machine technology modules – featuring revolving servo-based stations to provide synchronized article rotation and vertical stroke for the station, servo-based burner movements and electronically controlled burner and cooling air settings, oscillating stations, laser-measuring systems etc. This is why the welding station may move freely into the one or the other machine platform :
- welding functional station equipment – integrated into the füller-blowing system or into the stem-stretching system
- stem-stretching system: the number of stations is dependent on the process steps: welding and stretching require a sequential approach, while the blowing process can be in parallel to the welding
- any moil-removal system with the only difference, that for this application not only the servo-stations are revolving, but also the ring-burners may also be revolving to keep the heat-impact homogeneous
Rotarty –indexing – stem-stretching system
- the flexibility of one or more single-station systems locates the individual stations in the context of very low series, intricate designs and support for manual processes
- the indexing rotary table is synchronized with indexing rotary table blowing systems (below 10 pic/min output rate)
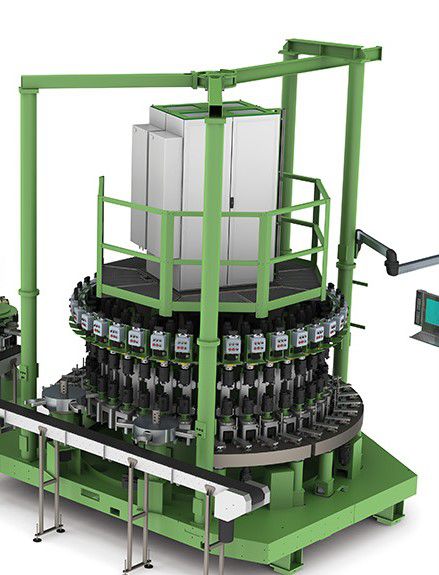
Rotarty–continuous –stem-stretching system with oscillating functional stations
- the continuous rotary system is adjusted to continuous rotary blowing systems with oscillating satellite stations
Combined with
- füller-blowing system
- füller hot-end handling
- … and certainly the MMC control
Specification Key Words
- electronic control of all process parameters
- looping-in on glass length parameters to provide stable quality
Combined with
- füller-blowing system
- füller hot-end handling
- … and certainly the MMC control
Specification Key Words
- electronic control of all process parameters
- looping-in on glass length parameters to provide stable quality