High Quality
Production Systems for
Optical, Technical and Crystal
Glasses
Melting and Feeding Technologies
Stream-Feeding (“drain”) System and Flow Control
The platinum feeding system has started out as a drain system targeting a very directcontrol of the glass temperature from the glass bath to the tip. It has successfully evolved into a segmented and highly specialized feeding system which provides optimum conditions for a controlled glass flow from the bottom of a forehearth to allow a stable furnace pull control as an additional glass consumer providing glass nuggets for in process cullet recycling strategies or to allow to remove circonia-enriched glass which accumulates on the bottom of the forehearth before the glass enters into the feeder; most importantly it is a very versatile system for feeding speciality glass for micro particles like beads, flakes, nuggets etc.
Directly heated platinum feeding system with flow control
- segmented system combing direct platinum heating with infrared heating as well as inductive heating technologies
- bottom “drain” technology to allow a defined glass flow from the lowest point of a furnace or forehearth –trapping and draining glass which is enriched with corrosion relics
- “drain” technology to supply fibre bushings with a directly heated interface system to control the glass flow with an active temperature control which is independent of the temperature conditions in the forehearth
- feeding “drain” system which taps glass from a core glass flow to reduce any boundary conditions for high-quality speciality glass feeding
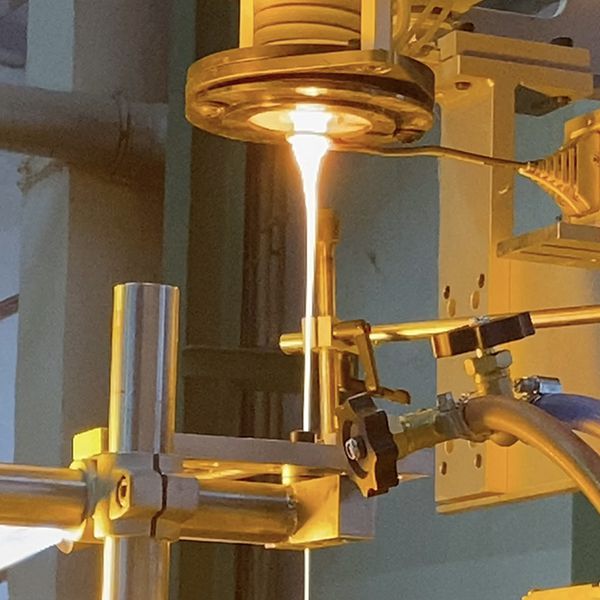
Combined with
- flow measuring system (diameter and temperature) and flow temperature control loop
- shear or roller system for dry cullet provision (in-process cullet recycling and pull rate stabilization)
- cutting wheel for micro-bead forming
- flaker for micro-particles
- and most prominently with the pre-melting system for liquid-in-liquid colouring systems
- … and certainly the MMC control
Specification Key Words
- full electric feeding system with on/off capability
- pull rate adjustment based on temperature as well as nozzle diameter adapationto extend the range of min/max. pull rate capability
Combined with
- flow measuring system (diameter and temperature) and flow temperature control loop
- shear or roller system for dry cullet provision (in-process cullet recycling and pull rate stabilization)
- cutting wheel for micro-bead forming
- flaker for micro-particles
- and most prominently with the pre-melting system for liquid-in-liquid colouring systems
- … and certainly the MMC control
Specification Key Words
- full electric feeding system with on/off capability
- pull rate adjustment based on temperature as well as nozzle diameter adapationto extend the range of min/max. pull rate capability